Different CNC machining processes will leave different machining surfaces finishes. Leaving those surface finishes as they are is the most cost-effective and straightforward finish. Beyond that, there are a few other surface finishes available like bead blasting and polishing. Machined surfaces can also be modified with coatings to increase surface hardness, increase lubricity, and provide corrosion resistance. Below is an overview of the various surface finishes and coatings that can be utilized with CNC machined parts.
SURFACE FINISHES CHART AS MACHINED
The chart below shows some CNC operations and what range of surface finishes (in RMS) can be expected. Note that smoother surface finishes are possible without changing the operation but may require different tooling and extended machine time (higher cost).
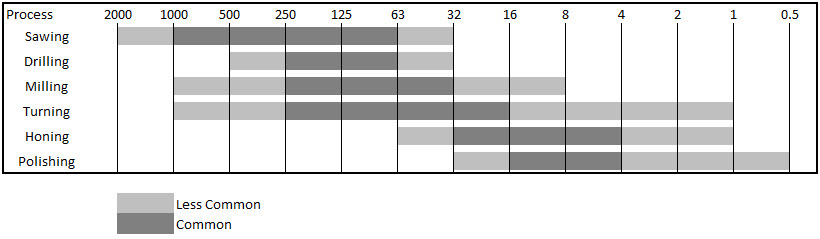
BEAD BLAST
Bead blasting is a manual process of applying small glass beads under high pressure to the surface of a component. The beads cause a light texturizing that does not damage the component; instead, it creates a matte type texture. Depending on how detailed the part is and if it requires isolated texturing, bead blasting may or may not have an effect on component cost.
POLISHED SURFACES
Polishing surfaces can either be done by hand or by utilizing various types of machine polishing equipment. Basilius can provide hand polish surfaces to your specification or a barrel finish. The barrel finish type polishing is done by using a centrifugal finisher. The finishing equipment provides an isotropic finish, meaning that the surface will be consistent on all sides of the part.
POWDER COAT
Powder coating is the process of applying powder-type paint to a component and then baking the paint onto the part. According to the Powder Coating Institute, it represents over 15% of the whole industrial finishing market. There are several options for powder coating, from color choice to texture. When designing a part, it is essential to keep in mind that powder coating adds paint to the surface of a part and will not provide an accurate surface like CNC operations. Critical areas can be masked off during the powder coating process in order to avoid critical dimension areas.
ANODIZING
Anodizing is a corrosion and, if specified, wear-resistant coating. It is most commonly associated with aluminum parts and comes in a broad array of colors. Anodizing tends to be slightly transparent, so it may be important to consider the CNC machine marks underneath. The anodized “layer” is consistent and thin (less than .002 inches thick). You will want to consider this when tolerizing your components.
OTHER COATINGS
There are several different alternative coating options that provide rust prevention, corrosion resistance, lubricity, surface hardness, and so on.